Ceramic dielectric filters have the advantages of small size, light weight, and large Q value. They have an absolute advantage in the application of 5G and have great development potential. The key material for producing ceramic dielectric filters is microwave dielectric ceramics.
One. What is microwave dielectric ceramics
Microwave dielectric ceramics refers to a new type of ceramic functional material used in microwave frequency circuits (mainly in the 300MHz ~ 300GHZ frequency band).
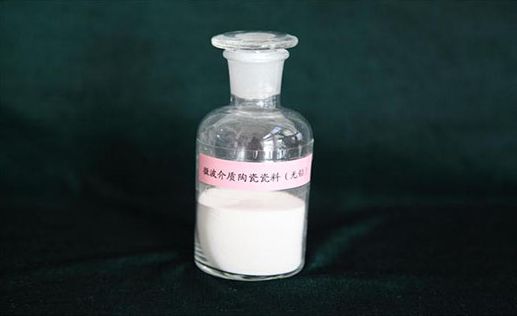
Picture: Microwave Dielectric Ceramic Porcelain
In the microwave frequency band, various polarization mechanisms are stable, and the dielectric constant of the material basically does not change with frequency. Therefore, according to the size of the dielectric constant, it can be classified into three categories: low dielectric, intermediate and high dielectric.
Low dielectric microwave dielectric ceramic systems such as Al2O3-TiO2 series and magnesium titanate series are used in fields with strict requirements on dielectric loss due to their high quality factors, such as satellite communications, military radars, etc.
Intermediate microwave dielectric ceramic systems such as (Zr, Sn)TiO4 have high Q value and low temperature coefficient of resonance frequency, which can be used to prepare dielectric resonators to solve the frequency drift problem of narrowband resonators.
High dielectric microwave dielectric ceramics can promote the miniaturization and integration of microwave communication equipment and resonators, and are widely used in high-capacity integrated circuits and communication equipment operating at low frequencies.
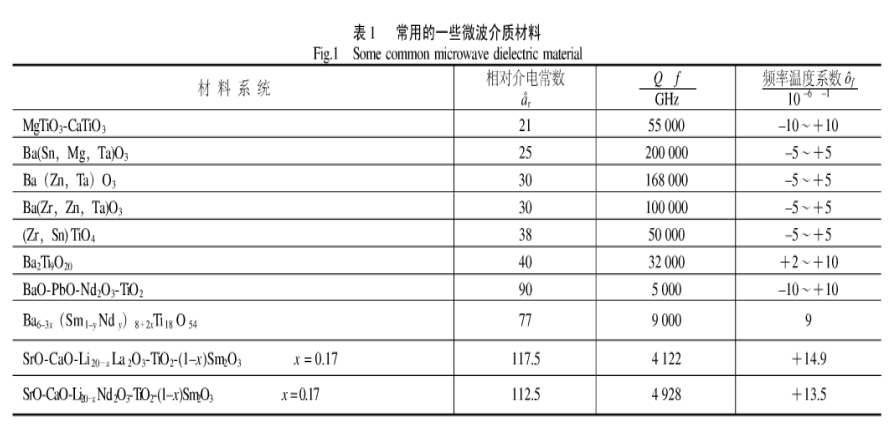
Microwave dielectric ceramic powder is not a single material, but a material system in which multiple materials are mixed in proportion. During the preparation process, rare earth oxides are also added. Many studies have shown that the doping of appropriate amounts of rare earth elements can improve the microwave medium The sinterability, density and dielectric properties of ceramics.
Two. Preparation method of microwave dielectric ceramics
The production methods of microwave dielectric ceramic materials include solid phase reaction method, sol-gel method, hydrothermal method, precipitation method and so on.
1. Solid phase reaction method
The solid-phase reaction method is a traditional process method, which has the advantages of mature process, easy operation, and high cost performance. It is suitable for mass production and is currently the most used method in industrial production. However, it has disadvantages such as high sintering temperature, easy formation of a second phase and abnormal growth of local crystal grains, which affect the microwave dielectric properties.
2. Sol-gel method
In the sol-sol method, a transparent sol is formed by a metal complex solution and an inorganic salt at a specific pH value, and then calcined to remove the organic components, and a uniform, very fine particle original powder can be obtained. The above improves the uniformity, structural uniformity and compactness of the ceramic composition, greatly reduces the ceramic sintering temperature and shortens the sintering cycle, can reduce or avoid the formation of the second phase, and is beneficial to improve the dielectric properties of the material. The cost of powder is high, the process is complex, the process parameters are not easy to control, and the production cycle is long, making it difficult to realize industrialization.
3. Hydrothermal method
The hydrothermal method is the reaction in a sealed pressure vessel, with an aqueous solution as the medium, the formation of the powder undergoes the process of dissolution to crystallization, without the need for expensive alkoxides, and many materials can be directly synthesized at low temperatures to avoid pre-burning. The grains grow, defects and impurities invade.
4. Precipitation method
The precipitation method is to use the soluble metal salts of each component element to form a solution in a certain proportion, add an appropriate amount of precipitating agent to uniformly precipitate the metal ions, and control the performance of the powder by adjusting the concentration and pH of the solution. A homogeneous mixture of oxides. The method is simple, easy to scale production, and low cost, but agglomeration or uneven components will affect the dielectric properties.
The preparation process of powder materials is technically difficult. For example, the hydrothermal method using barium carbonate as raw material includes dissolution, titanylation, drying, hydrothermal, and re-drying processes. Unreasonable acid-base control and impurity generation will damage the powder. The quality ultimately affects the performance of the filter.
Three. Material requirements for 5G ceramic dielectric filters
Microwave dielectric ceramics are widely used. Because of their good microwave dielectric properties such as low high-frequency dielectric loss, moderate dielectric constant, and low temperature coefficient of resonance frequency, they can be used as dielectric substrates, dielectric antennas, dielectric resonators, and Dielectric filters, etc.
The electromagnetic wave resonance in the 5G ceramic dielectric filter occurs inside the ceramic dielectric material, so higher requirements are put forward for the performance of microwave dielectric ceramic materials. The dielectric performance indicators of microwave ceramics are mainly dielectric constant, quality factor Q, resonance frequency temperature Three coefficients:
1. Suitable dielectric constant;
High dielectric constant can realize the filter size and miniaturization design, but the higher the dielectric constant is not the better, too high dielectric constant will affect the transmission loss, so it is necessary to consider the design requirements of the filter to select a suitable dielectric constant. The dielectric constant of microwave dielectric ceramics mainly depends on the crystal phase in the material structure and the preparation process.
2. High quality factor Q, low dielectric loss;
The higher the quality factor Q, the narrower the passband, the better the circuit selectivity, and the better the filtering function. The Q value is inversely proportional to the dielectric loss tanδ. The larger the Q value, the lower the filter insertion loss. The material structure is uniform, high density, uniform grain growth, reducing impurities and defects can increase the Q value.
3. Near-zero adjustable temperature coefficient of resonance frequency.
The temperature coefficient of resonance frequency is close to zero to achieve high stability and high reliability of the filter. The temperature coefficient of frequency is mainly determined by the linear expansion coefficient and dielectric constant of the material.
The ceramic powder determines the performance of the dielectric filter, and the powder formulation and preparation are more difficult. Only with a good material formula can we obtain high-Q dielectric ceramics under certain conditions of use. It can be said that our own powder formula is the core competitiveness of ceramic filter manufacturers. Filter manufacturers of powder formulations can make their own preparations by purchasing raw materials, avoiding purchasing from powder manufacturers, which not only saves costs, but also makes it easier to adjust the relevant parameters of the filter according to customer customized requirements.